What is a Fusion Splicer?
The optical fiber fusion splicer is a device that fusions
the end faces of the optical fiber at the high temperature (about 1,800°C)
generated by the arc, and immediately connects the two optical fibers placed on
the left and right sides of the device. The fusion splicer is an automatic
machine, you need to select the factory recommended settings or set the
splicing parameters yourself.
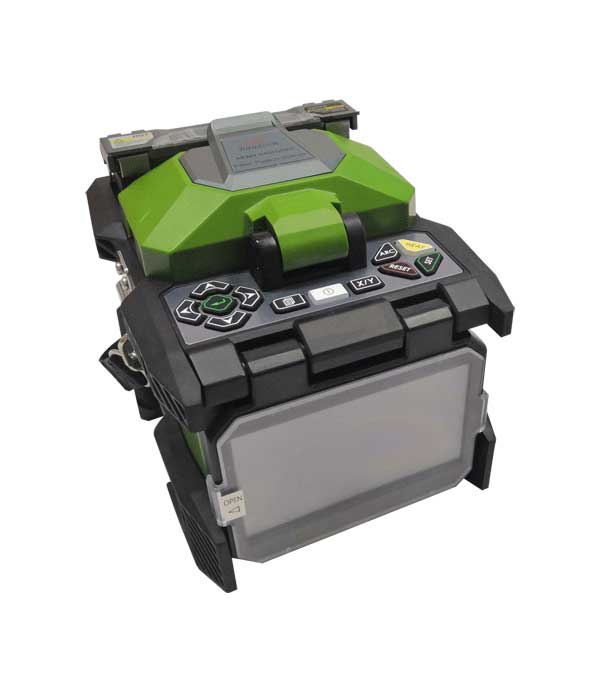
BD-FS-81 Optical Fiber Fusion Splicer
What is Fusion Splicing?
Fiber fusion splicing is the process of
permanently connecting two optical fibers together. Unlike fiber optic
connectors, fiber optic connectors are designed for easy reconfiguration on
cross-connect or patch panels.
There are two types of fiber fusion, mechanical
splicing and fusion splicing.
Mechanical splicing does not physically fuse the
two optical fibers together, but connects the two optical fibers in the sleeve
through a mechanical mechanism. Compared with fusion splicing, the insertion
loss and back reflection in mechanical splicing are worse. Mechanical fusion
splicing is mainly used for emergency repairs and fiber testing.
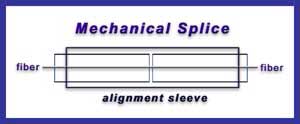
Mechanical Splicing
The second type of splicing is called fusion
splicing. In fusion splicing, two optical fibers are actually fused together by
arc welding. Fusion splicing is the most widely used splicing method because it
provides the lowest insertion loss and almost no back reflection. Fusion
splicing provides the most reliable connection between two optical fibers. Fusion
splicing is done by an automatic machine called a fusion splicer.
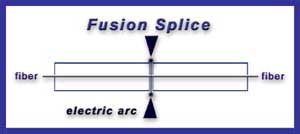
Fusion Splicing
How to Select a
Fusion Splicer?
It is necessary to understand the project type
of fiber fusion splicer and the requirements of each project. If you don't know
what your engineering requirements are, please look around to see which fiber
fusion splicer you are buying. You must first understand the requirements of
your project on the machine.
Although the main functions and characteristics
of various types of fusion splicers on the market are slightly different, the
elements of purchase are basically the same. Since the market demand for
single-core optical fiber fusion splicers is the largest, now take this product
as an example. According to the factors to be considered when purchasing, it is
not difficult to choose the most suitable fusion splicer for your measurement
requirements.
Price
When purchasing a fusion splicer, you must first
consider the product price range. The price of the splicer depends on many
factors, including splicing loss, display effect, battery life, etc.
Splice loss
For fusion splicers, splicing loss is the most
important indicator, which directly determines the quality and efficiency of
the project.
Battery life
Fusion splicers are mostly used in the field,
and battery life is very important. Generally speaking, a skilled operator can
splice up to 150 fibers a day. Therefore, the requirement for the battery is
that it can work continuously for at least 6 hours or can be connected and
heated more than 150 times.
Operability
The operators of the fusion splicer are mostly
ordinary workers, and ease of use is also an important factor.
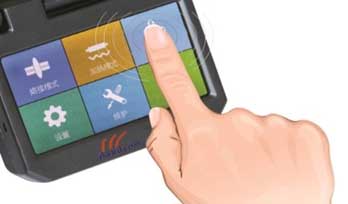
Heating time
The time for one optical fiber connection is
about 9s, and the time to heat shrink a 60mm standard heat shrinkable tube is
generally more than 35s. The heat shrinkage problem has become the biggest
factor restricting the further improvement of the overall construction
efficiency. In addition, the shortening of heating time also means that the
efficiency of the heater is improved, and the energy consumption of the battery
is reduced.
Welding time
Although the welding time has little effect on
the overall construction efficiency, the ability to complete high-quality
splicing in a relatively short time also represents the overall technical level
of the welding machine to a certain extent.
Display effect
The imaging effect of the optical fiber allows
the operator to have a more intuitive understanding of the entire splicing
process. In addition, the judgment of the fiber end face, the core adjustment,
and the evaluation of the splicing effect by the instrument are all based on
the image.
Volume and weight
For tools that are mainly used in the field,
miniaturization has always been the trend of development and improvement of fusion splicers. Smaller volume and weight will bring more convenience to users
in construction.
Interface function
At present, the main interfaces of the fusion
splicer are USB and VGA interfaces. Among them, the main function of the USB
interface is to perform system upgrades and data output; while the VGA
interface is used for video output, and an external display device with VGA
interface can be used to observe the real time display of the splicer. This
function is mostly used for training and teaching.
Types of Fusion Splicers
Single Fiber Fusion Splicer
Single fiber fusion splicers usually splice 250 micron fiber, but can also accommodate 900 micron sheathed
fiber, flat drop cable, and splice on connectors, which are also mainly used
for FTTH applications. A fiber is stripped, cleaned, cut, and then inserted
into the fiber holder. Repeat the same process for the other fiber to be placed
in the opposite fiber holder. Most of the newer single fusion splicer models
can be spliced and estimated attenuation (light loss) in less than 10 seconds.
Mass Fusion Splicer
Unlike fusing one fiber at a time, mass fusion
splicing can fuse all 12 fibers in a ribbon at a time. Many cables with high
fiber counts today contain 12 fiber subunits, and each subunit can be quickly
stripped. Splicing these fibers individually is very time consuming, mass fusion splicers can splice entire ribbons
simultaneously.
Core Alignment Fusion Splicer
Core Alignment Fusion Splicing is the most
commonly used splicing technology. A system of cameras, lenses, light sources,
and motors work together to optimize the position and alignment of the fiber
cores. The fibers are located in V-shaped grooves, allowing them to move in all
three axes, thereby providing core-to-core alignment optimization.
The ability to control the position of the core
of each fiber can improve the splicing performance, because the splicer can
compensate for the effects of fiber drift caused by pollution or core-cladding
concentricity mismatch.
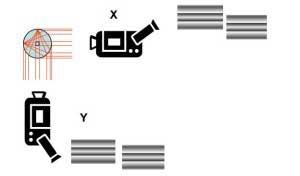
Core Alignment Fusion Splicing
Cladding Alignment Fusion Splicer
In the cladding alignment welding, a fixed
V-groove alignment method is used to align the cladding of the two optical
fibers. The fibers only move inward and outward. In addition to cutting
quality, alignment and subsequent fusion splicing performance are also severely
affected by fiber position, core cladding concentricity, and mode field
diameter. The position of the optical fiber is affected by the contamination of
the optical fiber or the V-groove and can be controlled by the operator.
Keeping the fiber and V-groove clean will ensure
that the fiber is in the best position. The splicing performance is also
affected by the core and cladding concentricity and MFD, but these are optical
fiber manufacturing parameters and cannot be controlled by the operator.
These factors are usually considered when
splicing new fibers with different fibers (such as single-mode G652.D to
G657.A).
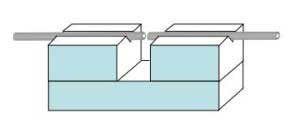
Cladding Alignment Fusion Splicing
Items Needed for Splicing
• Fiber Stripper
• Fusion Splicer
• Alcohol Wipes
• Fiber Splice
Connectors
• Fiber Cleaver
• OTDR
How Does Fusion Splicing Work?
Steps of Fusion Splicing
Step1 – Preparation
The first step in fusion splicing is to prepare
the fiber to be placed in the fusion splicer. Prepare the fiber by
stripping the coating, jacket, and tube, making sure that only bare fiber is
left. The polymer coating around the outer sheath and the inner glass fiber should
be removed. The exposed glass must be wiped with alcohol cleaner and placed on
the machine. A clean environment is essential for a good connection.
Step2 – Cleaving
The second step is to cleave the fiber. This is
different from cutting. You are breaking the fiber by introducing cracks. At
this point, the interrupt must be precise. The ends must be perpendicular and
smooth across the shaft. In other words, the interrupt must be
"clean". Before cutting the fiber, you must ensure that the stripped
fiber is cleaned with isopropanol or a similar fiber cleaning solution.
Step3 - Aligning and fusing
The third step is to align and fuse. Alignment
of two fiber optic splicer is finely adjusted until there is no or minimal or
no gaps are not aligned. The fusion splicer cleans both ends of the fiber optic
cable. The high intensity spark melts the end and burns any dust particles or
water droplets present at the end. Then the main spark generated by the fusion
splicer melts the end of the cable, so that the two cables are fused. Take
extra care when doing this so that only the core is melted and not the outer
cladding.
Step4 – Protect the Fiber
The last step is to protect the fused joint from
damage such as stretching or rough handling. You should place a protective heat
shrink sleeve around the fusion area. These sleeves are specially designed
protective sleeves to provide support for the joint area.
Maintenance of Fusion Splicer
In addition to cleaning the entire fusion splicer, you must also carefully
observe the electrodes and align them as they should. If any part is damaged,
you must replace it immediately.
These machines definitely have a heat balance
device. This protects the finished product from moisture and other types of
impurities. Clip-on protectors can also be used as an alternative method. However,
special attention must be paid to this area.
Conclusion
Therefore, this is everything you need to know
about fusion splicer. Baudcom is a company where you can
find really efficient fusion splicers which would make your job of splicing much
easier and effective.
Baudcom offers various
types of fusion splicer and all kinds of fiber tools. For more information,
please visit Baudcom.
Intersting Related article:What does a fiber splicer do?A Day in the Life of a Fiber Splicer
Can I Splice Two Optical Fibers with Different Cores by fiber fusion splicer?Here's How